Challenge
A regional refinery needed access to greater volumes and more diverse grades of crude oil. The original client assets were not capable of moving the desired product from the storage terminal in Oklahoma to the Northern Texas regional refinery. In addition to pipeline reversing, new booster facilities needed to be built to increase pumping capacity and flow rate to meet end user operational demands.
As part of updating the existing pipeline network and expanding with new assets, the client required control panel updates and automation for the entire operation. TIGA was selected for its expertise and successful delivery with similar process control and safety system projects.
Solution
TIGA transformed our pipeline asset automation into a highly reliable and dependable system. They have an eye for details and puts forth the effort to make sure projects are completed with high standards to quality and safety.”
– VP Engineering, Client
TIGA provided the design, programming, building, testing, installation, and commissioning of control panels for this pipeline project. This included the integration of the new instruments and devices.
GE Fanuc Emerson (RX3i PacSystem and Versamax) were used on 14 panels and Moxa MGate MB (Port RS-232/422/485 Modbus TCP Gateways) were used on 4 panels, totaling 18 panels to facilitate control of the new and upgraded sites.
Programming of a MCC Motor sync transfer logic from Toshiba VFD TOSVERT-300MV2 was implemented to coordinate lead/lag operation of two 2250 HP mainline pumps at each of the pipeline locations. Extra time was dedicated to setup a temporary testing station using one of the GE PLC’s to simulate the sync transfer.
TIGA also performed the programming of varied actions to adjust engineering design to the reality of pipeline operation.
Additional work provided included:
- Adding proximity warning/alarms to the three midpoint stations
- Motor current PID loop added at VFD control for two stations
- Current day, previous day and current month totalizers added to three of the stations
- Communication channel created at each station to act on destination point loss of permissive
- A pump differential pressure to detect no flow alarm logic was implemented for all mainline pumps of the pipeline
- Station retagging due to an error on the P&ID’s provided. This included changes to program tag and logic descriptions, drawings, and SCADA lists.
Project Execution Plan
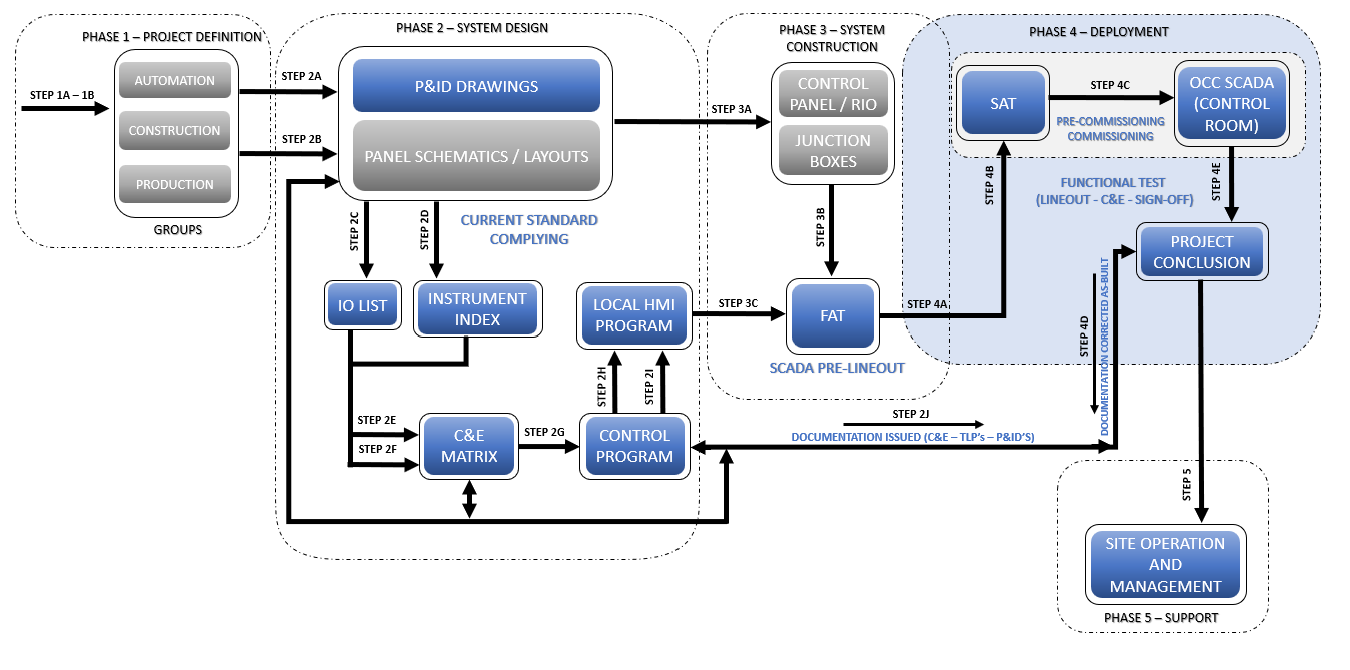
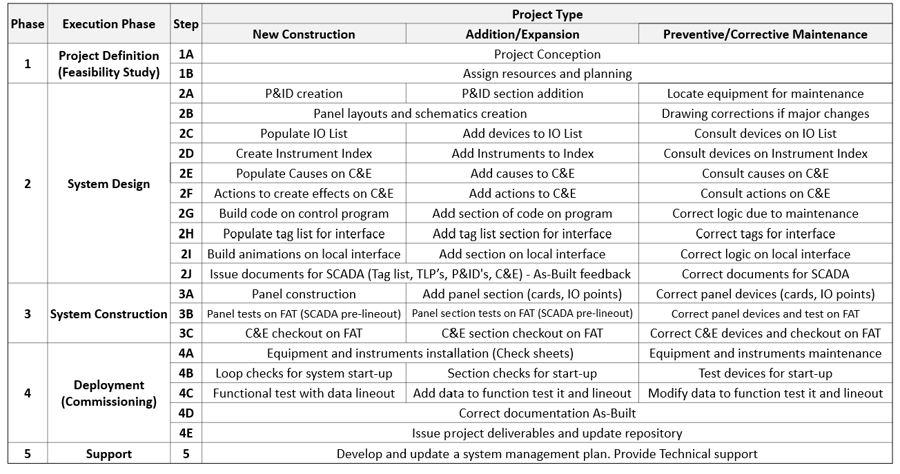
Value Delivered
“TIGA has been instrumental in supporting this large capital program. The knowledge and reliability of the TIGA team has improved the overall safety and control of our assets. The TIGA project manager has been a proven and invaluable resource and we look forward to their continued involvement.”
– Executive VP, Client
The one-year project completed with the successful opening of the new pipeline. The client’s operations group has expressed satisfaction with the functionality of the new system and the ease with which they can operate it after TIGA’s significant upgrade.
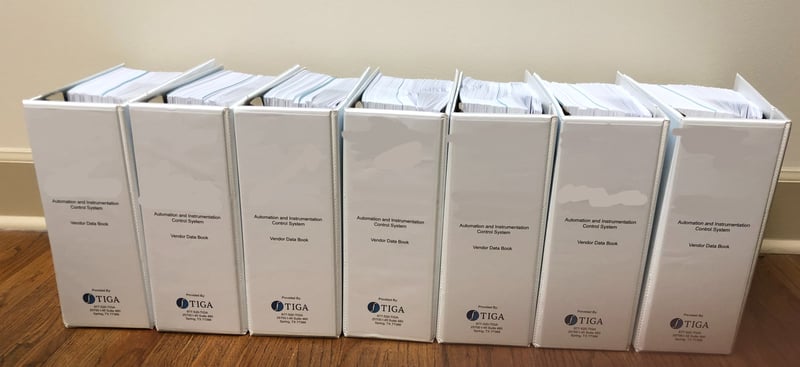
TIGA developed comprehensive job books, one per each of the seven stations, that included valuable engineering documentation such as: cause and effect, control narrative, IO List, SCADA list, panel drawings and schematics (including component data sheets and manuals), field device data sheets and manuals, and factory acceptance tests video and photo evidence.
Detailed documentation for electrical maintenance and operation crew’s benefit was also provided. Likewise, pipeline tracking and operation logic were created as part of the project, leveraging the new functionalities to operation. The engineering documentation templates TIGA used have eased many recurring operational tasks.
The project execution and results have led the client to propose new endeavors to collaborate on with TIGA.